Charcoal Canister Loading Station with Butane and Gasoline
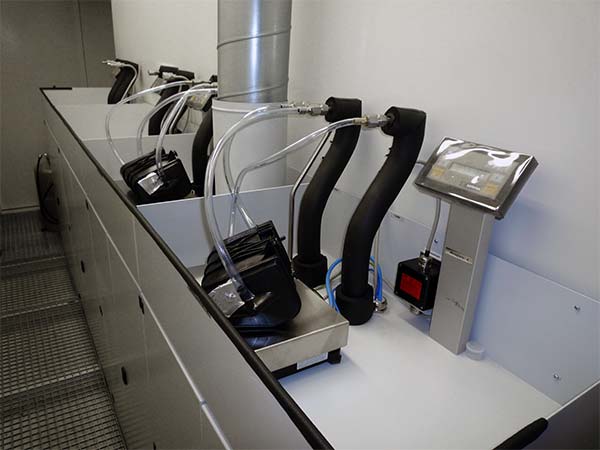
Charcoal canisters as used in automobiles to trap and hold gasoline vapours are loaded with butane and/or gasoline vapours. The system is designed to comply with US regulations CARB and EPA and EC-Norm 98/69/EC.
The systems are designed to load and purge up to 4 canisters simultaneously performing the following tests:
- Canister Preconditioning (1,5 x Working Capacity)
CARB Part III D 3.3.4
EPA §86.132-96(h)(1) - Canister Capacity Test (Breakthrough)
CARB Part III D 3.3.5 (a)
EPA §86.132-96(j)(1) - Canister Aging, multiple loading and purging
EU6
Loading:
The canister is loaded with a Butane/N2-mixture at a ratio of 50:50. Two Mass Flow Controllers (MFC) are used to control the gas flow. These MFCs have a control range of 10 to 500 SCCM corresponding for Butane in a flow rate of 1.5 to 75 g/min with 40 g/h as the standard loading rate. Any other loading rate and gas mixture within this range can be selected. For loading with gasoline a heated bubbler is filled with gasoline. N2 is used as as a carrier gas controlled by a MFC with a flow range of 10 to 500 SCCM, bubbler temperature adjustable up to 60°C. (MFCs with other control ranges on request). A secondary charcoal canister placed on a scale. Weight increase of 2 grams detects the breakthrough of the canister under test.
Option for loading with gasoline vapours: scale for the canister under test to record the weight increase of the canister.
Purging:
A venturi nozzle is used to draw ambient air through the canister. A mass flow meter at the air intake is used to measure the purge rate, range 0 to 50 SLM. The purge rate is controlled to 22,7 l/min by the amount of compressed air used to blow through the venturi nozzle. Air temperature and humidity are measured and recorded at the air intake.
Option: purge air preconditioning for a humidity range of 20 to 80% r.H.
Control:
The system is controlled by PC. The software is designed to perform all required tests in a fully automatic way and to takes all required recordings. The software is fully configured, tested and ready for use.
Safety measures:
- Gas warning system for hydrocarbons. The number of sensors depends on number of modules or other design requirements. At 20% lower explosion level all valves will close, at 40% lower explosion level the supply power to the system will switch off.
- Tubing for Butane and gasoline in stainless steel, compression type fittings, permanently tight.
- A pressure drop test is performed every time a canister is connected to the system. Canister loading will start only after this test is passed
- Systems for use with gasoline designed to be used in a explosion hazard risk area.